The Art of Improvement

Duration: 3 days
Category: Organisation
The Continuous Improvement Pressure cooker
Improvement starts with “I”.
Every single professional within the organization is faced with quality standards and ambitions. Now, while teams, departments and cross departmental groups of professionals aim to define and adhere to quality standards, there is a more intuitive, a less tangible, but more influential force that determines the overall quality of our products and services in your organisation.
This force is continuous improvement. Our continuous improvement cycle consists of the following 9 steps:
- Determine the need and area for improvement
- Assess current performance and analyze the organization’s environment to discover the cause of current performance
- Define the improvement objective
- Identify stakeholders and obtain commitment
- Define and organize diagnostics
- Generate, assess and evaluate solutions to accomplish the objective
- Production of implementation plans of the chosen solution
- Define controls for the new levels of performance
- Identify and overcome resistance to change
Program content
After implementation, the process starts again to create the continuous improvement cycle. It is essential for the organization that all of its parts have the same momentum and drive and are aware of individual roles in the improvement cycle. Their assessments, their improvement area identification and their actions define an elaborate continuous improvement in which the organization as a whole flourishes and excels.
The picture on the right depicts the structure of the program.
In more detail, the program can be broken down as follows:
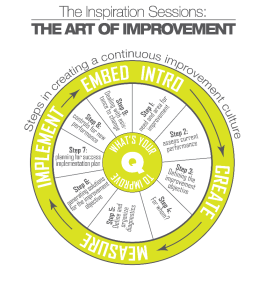
Part 1: Introduction to Continuous Improvement
- General introduction
- Introduction to Continuous Improvement; a variety of tools
- Identification of methodologies
- The Improvement Cycle (Plan-Do-Check-Act)
- Implication session:
- What can we learn from all of these methods?
- Inventorization assignment
- Characterizing the organization
- Step 1: the need and area for improvement
Part 2: Applying and creating your own methodologies
- Defining the Continuous Improvement cycle
- How are we doing?
- Step 2: assess current performance
- Research and analysis of the organization’s environment to discover the cause of current performance
- Assessing current performance
- Implication session step 1 and step 2:
- Inventorization assignment
- Discussion and definition
- What to improve and for whom?
- Step 3: Defining the improvement objective
- Step 4: For whom?
- Stakeholder analysis
- Obtaining commitment
- Implication session step 3 and step 4:
- Inventorization assignment
- Step 2: assess current performance
Part 3: Measuring success
- How to measure the success of the improvement process?
- Step 5: Define and organize diagnostics
- Benchmarking, Types and the Improvement Cycle (PDCA) Key Performance Indicators (KPI’s), Standard Operating Procedures (SOP’s) and the change environment
- Implication session step 5:
- How we know when we are improving?
- Inventorization assignment
- Step 5: Define and organize diagnostics
Part 4: Effective implementation
- Step 6: generating solutions to accomplish the improvement objective
- Solutions to generate improvement
- Assessing and evaluating available solutions
- The Evaluation Matrix
- Best Practice:
- Case examples
- Tips and tricks
- Step 7: planning for success, the implementation plan
- Avoiding the pitfalls
- Step 8: defining and applying controls for new levels of performance
- Implication session:
- How to achieve improvement?
- Inventorization assignment
Part 5: Embedding Continuous Improvement in the organisation
- Stakeholder management approaches
- Step 9: identify and overcome resistance to change
- Project management for continuous improvement
- How to embed the continuous improvement methodology?
- Implication workshop:
- Defining the projects, plan for execution and control
- Applying Ishikawa, Lean, 5W1H for effective processes
- Step 9: identify and overcome resistance to change
How can this work for your
company and people?
The objectives of this course for participants are:
- Understanding the tools to achieve continuous improvement
- Analysis of environment and processes
- Understanding, defining and maintaining quality standards
- Skills/competencies to continuously improve their work and activities
- The essence of quality control and auditing practice
- Identifiable results through precourse inventorization and KPI definition
- Participants interact with and learn from each other, generating integrative sales and business development approaches and higher effectiveness and organizational consistency
“Arvid helped us to redefine our commercial strategy. His business wisdom, his energy and sense of humor made it wonderful to work with him and led to clear decisions, executable plans and 50% growth.”
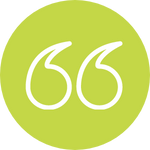
Michel
CEO, Intelligent Automation
“We always look forward to having him around as our organization becomes a little brighter when he is around…”
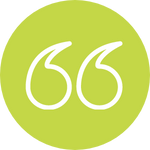
Jessica
Learning & Development, Maritime
“Our learning and development has improved greatly because of their inspiration and energetic sessions.”
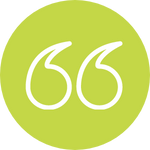
Mohammed
HR Manager, Telco
“Extraordinarily engaged and committed people.”
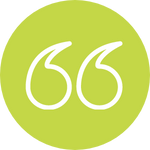
Linda
HR manager, Education
“A very effective, no-nonsense approach to our strategy and implementation through their Pull Principle…”
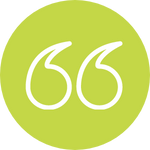
Sandra
Director, Cultural Organization
“Their consultants are different from the ones I have worked with in other firms; Q management doesn’t stop till the job is done and the results achieved.”
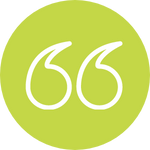
Saif
SCM manager, Oil & Gas